Циркуларне заједнице у Србији
Циркуларна економија је модел привреде који штеди и обнавља природне ресурсе и енергију, продужава коришћење материјала и производа и смањује отпад. У последњих 50 година потрошња ресурса на глобалном нивоу порасла је четири пута, уз неодржив пораст потрошње енергије, емисија гасова са ефектом стаклене баште и количине генерисаног отпада. Тренутно је мање од 9% светске економије базирано на циркуларним принципима, а ови принципи ће бити нужност за одрживу економију будућности.
Ради подстицања и промовисања циркуларне економије у локалном контексту, Министарство заштите животне средине и УНДП у партнерству спроводе пројекат “Смањење угљеничног отиска локалних заједница применом принципа циркуларне економије у Републици Србији – Циркуларне заједнице”, уз финансијску подршку Глобалног фонда за животну средину (ГЕФ), од марта 2022. године до марта 2027. године.
Више
Циљ пројекта:
Подстицање развоја и подршка спровођењу циркуларних идеја, пословних модела и производа јавних и приватних предузећа, ради смањење угљеничног отиска локалних заједница у Србији.
Фокус пројекта:
- Успостављање подстицајне јавне политике и институционалног оквира усклађеног са политикама ЕУ о циркуларној економији, укључујући обуке за побољшање знања и вештина кључних актера, као и подстицање широког учешћа заједнице у развоју и спровођењу таквих политика;
- Успостављање Платформе за иновације у циљу смањења емисија гасова са ефектом стаклене баште у локалним заједницама (Low Carbon Communities Innovation Platform – LCCIP) како би се идентификовале и подржале нове пословне идеје, производи, инвестиције у области циркуларне економије и ефикасног коришћења ресурса;
- Пилот инвестиције у области циркуларне економије;
- Ширење знања и подизање јавне свести о значају циркуларне економије.
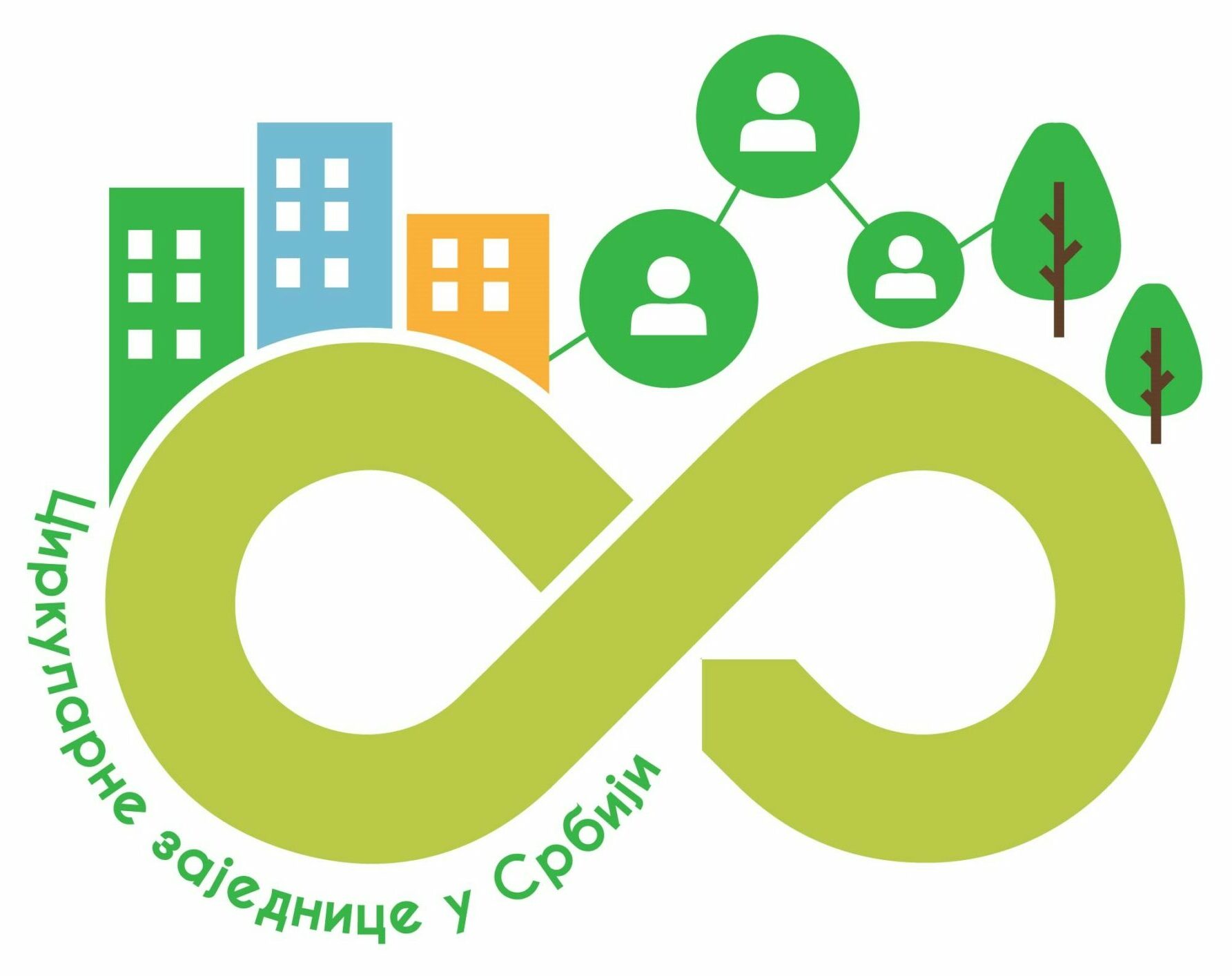